INTRODUCCIÓN
Actualmente el cuidado y preservación del medio ambiente es uno de los temas más importantes a nivel mundial. Debido a la sobreexplotación y el agotamiento de los recursos minerales y en beneficio del medioambiente, la comunidad científica se ha centrado en la búsqueda de nuevas alternativas para la recuperación, reutilización y reciclado de metales de fuentes secundarias como residuos, escorias, relaves, etc. Por sus características el aluminio es un metal que puede ser reciclado en repetidas ocasiones, sin perder sus propiedades1). La Industria Europea del
Aluminio en su plan de acción circular de aluminio (The Circular aluminum action plan, European Aluminium Association, 2019ª) tienen como estrategia mejorar la recolección, clasificación y reciclaje de la chatarra ya que tiene grandes beneficios económicos y ambientales, pues la producción de aluminio reciclado solo requiere alrededor del 5 % de la energía necesaria para producir la misma cantidad de aluminio primario2,3. Reciclarlo cambia el equilibrio hacia una mayor sostenibilidad, se estima que se duplique la cantidad de aluminio para reciclarse para 20503,4, por lo que producir aluminio a partir de chatarra representa una alternativa viable, trayendo consigo grandes beneficios al medio ambiente, ya que no solo se está reciclando un residuo, sino que también disminuye la energía requerida para producirlo, impactando directamente en la disminución de los gases de efecto invernadero5,6.
Tan solo alrededor de la mitad de la chatarra de aluminio al final de su vida útil se recicla en EE. UU.5, por lo que es importante promover el reciclado y la reutilización de la chatarra de aluminio, como una alternativa para la preservación y cuidado del medio ambiente. La utilización de chatarra de aluminio ya está siendo estudiada gracias a las ventajas medioambientales que esta alternativa representa, por ejemplo; se desarrollaron colectores solares verticales de aire (VSAC) para ser utilizados en edificios, utilizado latas de bebida de aluminio como aletas para mejorar la eficacia del sistema colector7.
En otros trabajos relacionados: Se reciclo una mezcla de aleaciones de aluminio de aviones de desecho concluyendo que se pueden obtener aleaciones de aluminio 7075 de alta calidad8. Se realizó un estudio en el que se propuso un método de purificación para eliminar las impurezas del aluminio reciclado9. También se hizo un estudio de la evaluación ambiental del proceso de reciclaje de cables, los datos fueron tomados de una planta de reciclaje en Francia. El proceso se basó únicamente en la separación mecánica y clasificación óptica en cables trituradores y el estudio demuestra enormes beneficios ambientales para el aluminio reciclado en comparación con el aluminio primario10.
Por otra parte, uno de los productos de aluminio, que se obtiene a partir de la bauxita, es el sulfato de aluminio Al2(SO4)3, un sólido blanco de cristales lustrosos. Puede tener muchas estructuras, aunque sus hidratos tienden a adoptar el sistema cristalino monoclínico. Es una sal muy soluble en agua, y en la naturaleza es raro encontrarlo en su forma anhidra. Usualmente se encuentra hidratado bajo la forma de sulfato de aluminio octadecahidratado [Al2(SO4)3.18H2O] o hexadecahidratado [Al2(SO4)3.16H2O].
De la gran cantidad de acciones para el cuidado del medio ambiente, se considera de suma importancia el tratamiento de aguas, donde para dar cumplimiento a las legislaciones existentes, se hace uso de diversos agentes químicos que ayuden a cumplir los límites máximos permitidos, y dentro de estos, la selección del coagulante es un proceso en el que se consideran varios criterios de modo que se garantice las óptimas condiciones del tratamiento en el equipo de clarificación con la consecuente mejor calidad del agua tratada y a un menor costo.
Los coagulantes se clasifican en dos grupos: inorgánicos y orgánicos. Los coagulantes inorgánicos (químicos) más usados en el mundo para el tratamiento del agua, que pueden ser simples o polimerizados, son el sulfato de aluminio, las sales de hierro y la cal; cada coagulante tiene un valor de pH específico donde ocurre la mínima solubilidad y la máxima precipitación11.
Si bien los usos de diversos coagulantes presentan ventajas y desventajas, el sulfato de aluminio sigue siendo una opción para la coagulación o floculación en el tratamiento de aguas. Al mezclarse con el agua (potable, servida o de desecho), el sulfato de aluminio origina hidróxido de aluminio, el cual forma complejos con los compuestos y las partículas en suspension acelerando su sedimentación y la remoción de turbidez y color. Postalochi, L. et al, demostraron que el Al2(SO4)3 es uno de los coagulantes más utilizados para el tratamiento del agua12.
La fabricación de sulfato de aluminio es de suma importancia desde el punto de vista económico, debido a los bajos costos de materia prima que se utiliza. Los subproductos generados en el proceso de fabricación tienen un destino útil y por lo tanto un margen de recuperación adicional13. El sulfato de aluminio comercial Al2(SO4)3 normalmente se produce de manera industrial utilizando rocas de bauxita como materia prima (20-30% del contenido es aluminio). Sin embargo, depender de la bauxita tiene limitaciones, ya que está disminuyendo la disponibilidad de este mineral a nivel mundial y apenas está presente en cantidad comercial en la mayoría de los países en desarrollo14.
El objetivo del presente proyecto es diseñar un proceso para la fabricación de un clarificador-coagulante para tratamiento de aguas y aguas residuales, a partir de chatarra de alumini
METODOLOGIA
En la figura 1, se presenta la metodología seguida para el desarrollo del proyecto, en forma de Diagrama de Flujo.
Como primer paso se hizo la investigación documental de lo relacionado con el Al, fundición de Al y el proceso de fabricación del sulfato de aluminio. En seguida se realizó el diseño del horno y se determinaron los requerimientos del proyecto. Para la fabricación del primer prototipo de horno (figura 2), se utilizaron los siguientes materiales: Tanque de gas refrigerante de 6.8 Kg, cemento blanco y arena.
La primera paila de fundición se fabricó con un envase de extinguidor, mientras que la segunda se fabricó con acero inoxidable, ambas de 4” de diámetro y 10 cm de altura.
Para el segundo prototipo; tanque de gas, aislante térmico de fibra cerámica para el interior, exterior y tapa, malla de acero inoxidable para soporte del aislamiento interior, lámina galvanizada para la cubierta exterior y tapa. En la figura 3, se presentan el diagrama esquemático del horno e imágenes del segundo prototipo.
Para las pruebas de funcionamiento (Figura 4) se utilizaron los siguientes materiales y equipos: Gas LP, 500 gr de chatarra de Al (latas), copelas de barro, balanza Torrey EE30 serie 208 de 30 Kg y bascula de triple barra OHAUS de 26120 gr, quemador Flamineta para gas LP con boquillas de 1 y 1¼ ”, soporte para paila (tubo galvanizado 7 cm de diámetro x 7.5 de altura X 1 mm de espesor), payonera de fierro de 4 cavidades, ganchos para vaciado de la paila, equipo de seguridad como: caretas y lentes, guantes y mandil, y 4 Termómetros con las siguientes marcas y características: CEM DT-8819 Infrarrojo de -50 a 750 °C, de mercurio Allafrance de -20 a 250 °C y Gain Express Digital tipo K de 2 canales de -50 a 1300 °C.
Para la fabricación del sulfato de aluminio, se utilizaron placas de Al de 30 x 60 x 3 mm, granalla de Al, botones de Al obtenidos por la fundición de chatarra, ácido sulfúrico comercial (98%) y material de laboratorio. También un rectificador Kaselco de 50 V y 10 A de CD y un equipo para Prueba de Jarras.
El cálculo del % de recuperación de Al, se hizo considerando el peso del aluminio recuperado x 100 y dividido entre los 500 gr que se alimentaron de chatarra Ecuación 1.
Mientras que la eficiencia energética se calculó considerando el calor aprovechado x 100, dividido entre el calor disponible Ecuación 2.
Dónde: W es peso, Cp es el calor especifico del Al (910 J/kgoC), Cf el calor de fusión del Al (394,000 J/kgoC), y PC el poder calorífico del gas LP (49,650 J/kgoC).
El siguiente paso fue la selección de un Diseño Experimental, se eligió un 22 con dos replicas, los factores seleccionados fueron: el tamaño de la boquilla del soplete con dos niveles 15/16” y 1-3/16”, y soporte para la paila, con dos niveles “con” y “sin”. Luego se corrieron las pruebas del Diseño Experimental y se analizaron los resultados obtenidos.
Para la fabricación del sulfato de aluminio a partir de Al, primero se elaboró una calculadora de las cantidades estequiometrias en Excel. Se hicieron cuatro pruebas: Prueba 1, obtención del sulfato de aluminio por Electrocoagulación (EC) de placas de aluminio con solución de ácido sulfúrico. Se utilizaron placas de aluminio de 28 x 58 x 3 mm y un rectificador Kaselco de 50 VCD y 20 A. Se aplicaron 40 VCD y con una corriente de 1.3 A; Prueba 2, obtención de Al(OH)3 por medio de electrocoagulación utilizando una placa de Al y su posterior conversión a Al2(SO4)3, por reacción con H2SO4; Prueba 3, reacción de placa de Al con H2SO4; Prueba 4, reacción de granalla de Al2O3 con H2SO4, la Prueba 5, reacción de granalla de Al con H2SO4 y la Prueba 6 los botones de fundición obtenidos en el horno fabricado con H2SO4. En caso de resultados satisfactorios se prueba el producto obtenido mediante Prueba de Jarras.
RESULTADOS
El segundo prototipo del horno funciono perfectamente permitiendo realizar las corridas del Diseño experimental (DE).
El procedimiento para la realización de las pruebas se fue modificando de acuerdo a las condiciones, a la experiencia adquirida y a los resultados. El procedimiento fue: pesar 500 gr de latas, pala, paila y tanque de gas. Cuando corresponde poner el soporte de la paila. Seleccionar la boquilla del soplete correspondiente, colocar el quemador encendido en el ducto verificando que no haya obstrucción a la entrada de aire y precalentar el horno y paila durante 10 min para alcanzar los 680 °C. Durante la prueba se monitorea la temperatura ambiente, la interna, la de los gases de combustión y la externa. Se alimentan las latas. Cuando este fundiendo, retirar la escoria. Al terminar de alimentar las latas dejar la temperatura en aproximadamente 680 °C por 10 min más y luego apagar el quemador. Sacar la paila del horno con el soporte. Inclinar la paila con el soporte y con el gancho para retirar el resto de escoria. Vaciar el Al a la payonera. Dejar enfriar. Pesar pala, paila, y botones de Al.
Las pruebas de fundición se realizaron de acuerdo con el DE seleccionado (22), y se corrieron en orden aleatorio. Los resultados se presentan, en el orden estándar, en la Tabla 1.
Tabla 1: Resultados del Diseño experimental 22
Orden | Soporte | Boquilla | % Recuperación de Al (1) | % Recuperación de Al (2) | Promedio % Recuperación | Eficiencia Energética (%) (1) | Eficiencia Energética (%) (2) | Promedio Eficiencia Energética (%) |
---|---|---|---|---|---|---|---|---|
1 | Sin | Chico | 68.76 | 64.55 | 66.66 | 55.766 | 56.242 | 56.00 |
2 | Con | Chico | 75.87 | 60.07 | 67.97 | 54.333 | 63.349 | 58.84 |
3 | Sin | Grande | 83.52 | 84.05 | 83.79 | 48.994 | 57.873 | 53.43 |
4 | Con | Grande | 80.20 | 95.48 | 87.84 | 61.058 | 65.424 | 63.24 |
De la Tabla 1 de datos se concluye que los mejores resultados, para el % de Recuperación de Al y de Eficiencia energética se obtuvieron utilizando soporte para la paila y usando la boquilla grande del quemador. Estos resultados fueron confirmados con el programa estadístico MINITAB.
Para el % de Recuperación de Al (figura 5), el ANOVA indica que únicamente el tamaño de la boquilla afecta significativamente el % de recuperación de aluminio, ni el uso del soporte, ni la interacción entre ambos afectan la respuesta. Los signos positivos de la ecuación de regresión, nos indica que para tener el mejor % de recuperación debemos tener los dos factores en su nivel alto, es decir boquilla grande y utilizando el soporte, lo cual concuerda con los resultados de las pruebas. La R2 de 73.77%, nos indica que hay una correlación relativamente fuerte entre los factores y la respuesta.
Para la eficiencia Energética el ANOVA (Figura 6), indica que únicamente el uso del soporte afecta significativamente la respuesta. Ni el tamaño del quemador, ni la interacción entre ambos afectan la respuesta. Al igual que con él % de recuperación, los signos positivos de la ecuación de regresión indican que, para tener la mejor Eficiencia, debemos tener los dos factores en su nivel alto, es decir, utilizando el soporte y la boquilla grande. La R2 de 49.3%, nos indica que hay una correlación débil entre los factores y la respuesta.
En la figura 7, se presentan los resultados del análisis de escoria de la fundición de Al por Absorción Atómica (AA) y por Difracción de Rayos X (XRD), ambos externos. Los principales componentes son: Al, Mg y Fe. Lo que indica que aún podría refinarse más y mejorar el rendimiento.
Los resultados para la fabricación del sulfato de aluminio a partir de Al, fueron para la Prueba 1, obtención del sulfato de aluminio por electrocoagulación de placas de aluminio con solución de ácido sulfúrico. Se utilizaron placas de aluminio de 28 x 58 x 3 mm y un rectificador Kaselco de 50 VCD y 20 A. Se aplicaron 40 VCD y con una corriente de 1.3 A. El sulfato de aluminio presento coloración, por lo que se tuvo que filtrar. En la Prueba de Jarras los resultados fueron satisfactorios.
Prueba 2, obtención de Al(OH)3 por medio de electrocoagulación utilizando una placa de Al y su posterior conversión a Al2(SO4)3, por reacción con H2SO4 (figura 8).
Prueba 3, obtención de Al2(SO4)3 por medio de reacción de una placa de Al con solución de H2SO4. Los resultados de la producción y de la prueba de jarras fueron excelentes.
Prueba 4 y Prueba 5, reacción de granalla de Al2O3 y granalla de Al con H2SO4; los resultados de ambas pruebas no fueron buenos, y aun con un tiempo de reacción de días, reaccionaron solo parcialmente con la aparición de un precipitado negro.
Prueba 6, reacción de los botones de fundición obtenidos en el horno fabricado, con H2SO4 (figura 9 ). Tampoco hubo resultados favorables, con un tiempo de reacción de días se logró la formación del Al2(SO4)3, sin embargo, también se presentó la formación de un precipitado negro, posiblemente sulfato u oxido de fierro proveniente de los componentes de la lata. Tuvo que filtrarse y tuvo buen desempeño en la prueba de coagulación - floculación.
DISCUSIÓN
En vista de los resultados obtenidos, se decidió cortar los botones de la fundición, en forma de placas para utilizarlos como electrodos en la EC, se procedió a la aplicación de VCD para la formación de Al(OH)3, y luego a la producción de Al2(SO4)3 (figura 10). Con muy buenos resultados, en cuanto a tiempo de reacción, sin formación de precipitado negro y prueba de jarras.
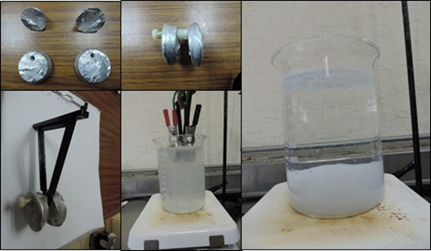
Figura 10: Obtención de Al2(SO4)3 por EC utilizando botones de la fundición de chatarra de Al, y reacción con solución de H2SO4.
La figura 11 , muestra el proceso para la producción de sulfato de aluminio a partir de chatarra de Al, considerando que la composición de las latas de aluminio puede variar y requerir filtración.
CONCLUSIONES
Se cumplieron los objetivos del proyecto de diseñar un horno para la fundición de chatarra de aluminio y se diseñó un proceso para la producción de sulfato de aluminio. Se aplicó un diseño experimental para buscar las mejores condiciones de operación del horno; tanto para la recuperación de aluminio como para la eficiencia energética. El promedio obtenido para él % de recuperación de Al fue de 76.56, y para la Eficiencia Energética de 57.88 %. Mientras que los valores máximos obtenidos para la recuperación del Al, con las mejores condiciones de operación fueron 95.48 y 65.42 % respectivamente. Son muchos los componentes de las latas de aluminio e incluyen impurezas que pueden afectar el proceso. Aunque los principales son: Al, Mg y Fe. Lo que también indica que aún podría refinarse más y mejorar el rendimiento.